Did you know that over 60% of DIY enthusiasts prefer building their own workbench instead of buying one? I was one of them. My journey began when I realized my chiseling and saw work needed a more stable surface. That’s when I discovered the value of using woodworking bench plans to create my own version.
Inspired by Chris Schwarz’s designs, I started crafting a plan that combined historic craftsmanship with modern functionality. Building my own workbench wasn’t just about saving money—it was about creating something tailored to my needs. Plus, it’s incredibly rewarding to use a tool you’ve built yourself.
In this article, I’ll share my experience and provide you way to download 16,000 woodworking plans.
Key Takeaways
- Building your own workbench ensures stability and precision.
- Custom designs allow you to tailor the workbench to your needs.
- Creating a workbench is more cost-effective than buying one.
- Historic and modern designs can inspire your project.
- A free PDF plan is available to guide you through the process.
Getting Started with Woodworking Bench Plans
Starting a workbench project can feel overwhelming, but breaking it down makes it manageable. The first step is understanding the basic principles behind a sturdy and functional design. I found that researching different styles and reading Chris Schwarz’s book on design theory gave me a solid foundation.
Before purchasing any material, it’s essential to read through the instructions thoroughly. This helps you visualize the entire project and identify potential challenges early. Clear guidelines ensure you stay on track and avoid costly mistakes during assembly.
Here’s a video I found useful if you are more of a visual learner:
Selecting the right tool and material is equally important. I recommend making a checklist of everything you’ll need before starting. This not only saves time but also ensures you have everything ready when you begin building your bench.
Early planning is key to a successful workbench build. By taking the time to understand the design and gather the necessary resources, you’ll set yourself up for a smoother and more enjoyable experience. Remember, a well-planned project is half the battle won.
Gathering Materials and Tools
The foundation of any successful project lies in proper preparation. Gathering the right material and tool is the first step toward building a sturdy and functional workbench. Without quality components, even the best design can fall short.
To ensure everything goes smoothly, I recommend creating a detailed checklist. This will help you stay organized and avoid last-minute trips to the store. Planning ahead is the best way to save time and effort. You can also try these cool woodworking projects to get ideas on how to start.
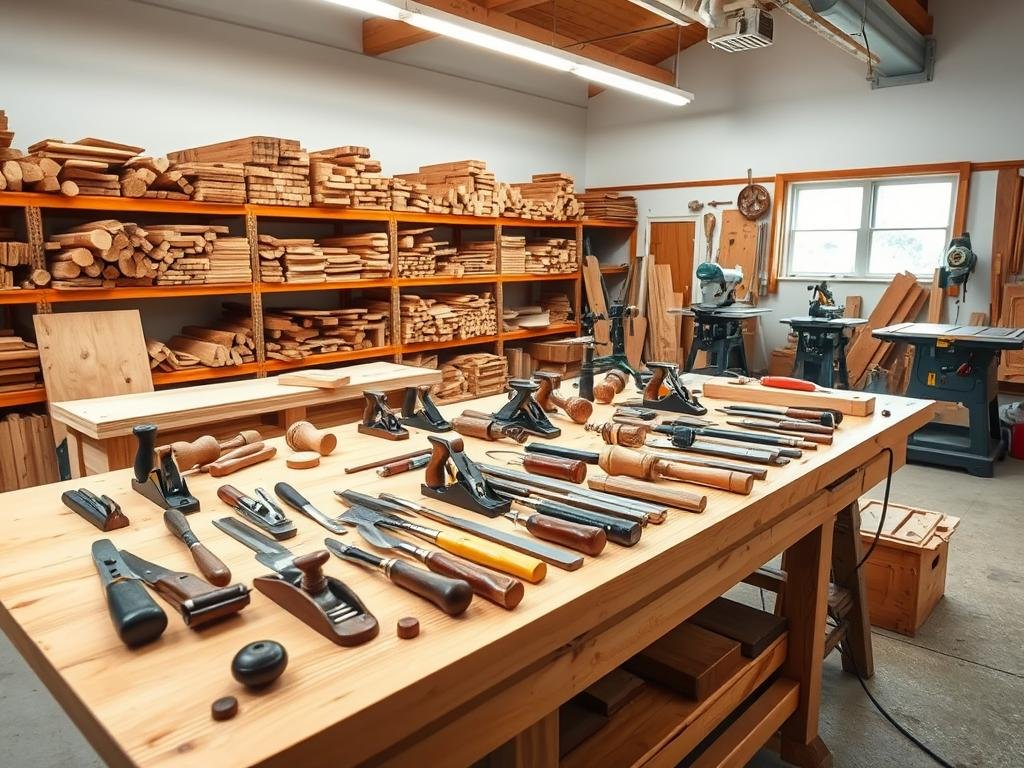
Essential Lumber, Hardware, and Supplies
Choosing the right lumber is critical. I prefer using kiln-dried and straight construction-grade lumber, such as 2x12s from big box stores. This ensures stability and minimizes warping over time.
Hardware is equally important. High-quality screws and fasteners play a big part in the structural integrity of your workbench. Don’t skimp on these—they’re the backbone of your build.
Recommended Tools and Equipment
Having the right tool makes all the difference. Here’s a list of what I used:
Tool | Purpose |
---|---|
Circular Saw | Cutting lumber to size |
Drill | Creating pilot holes and driving screws |
Router | Shaping edges and creating grooves |
Clamps | Holding pieces together during assembly |
Investing in quality tools and materials ensures your workbench will stand the test of time. With the right preparation, you’re ready to move on to the next step.
Planning Your Workbench Design
Designing a sturdy workbench starts with careful planning and attention to detail. The right design ensures stability, functionality, and long-term durability. Every step in the process, from leg placement to joint construction, plays a crucial role in the final product.
Design Considerations for Stability and Functionality
When planning your workbench, focus on the bottom and top structures. The legs must be placed strategically to support weight evenly. I found that using mortise and tenon joints at the end of the bench significantly improves stability.
Here are some key design elements to consider:
- Leg Placement: Properly spaced legs prevent wobbling and ensure even weight distribution.
- Mortise and Tenon Joints: These joints at the end of the bench add strength and durability.
- Top Surface: A flat and sturdy top is essential for precision work.
In my own project, I adjusted the design to include thicker legs and reinforced joints. This small change made a big difference in stability. Each step of the design process influences the final assembly and functionality.
Taking the time to plan your design ensures a smoother build and a more reliable workbench. With these considerations in mind, you’ll create a tool that meets your needs and stands the test of time.
Step-by-Step Construction Process Overview
Accurate measuring and cutting are the foundation of any successful build. When I started my project, I knew that careful preparation would make all the difference. Here’s a detailed breakdown of the steps I followed to ensure a smooth and efficient process.
Preparing Lumber and Setting Up Your Shop
Before diving into the build, I took the time to prepare my workspace. Handling large pieces of lumber requires a clear and organized area. I made sure my shop was clean and free of clutter to avoid accidents and ensure precision.
I also gathered all the necessary tools and materials. This included a circular saw, clamps, and measuring tape. Having everything ready beforehand saved me time and kept the project on track.
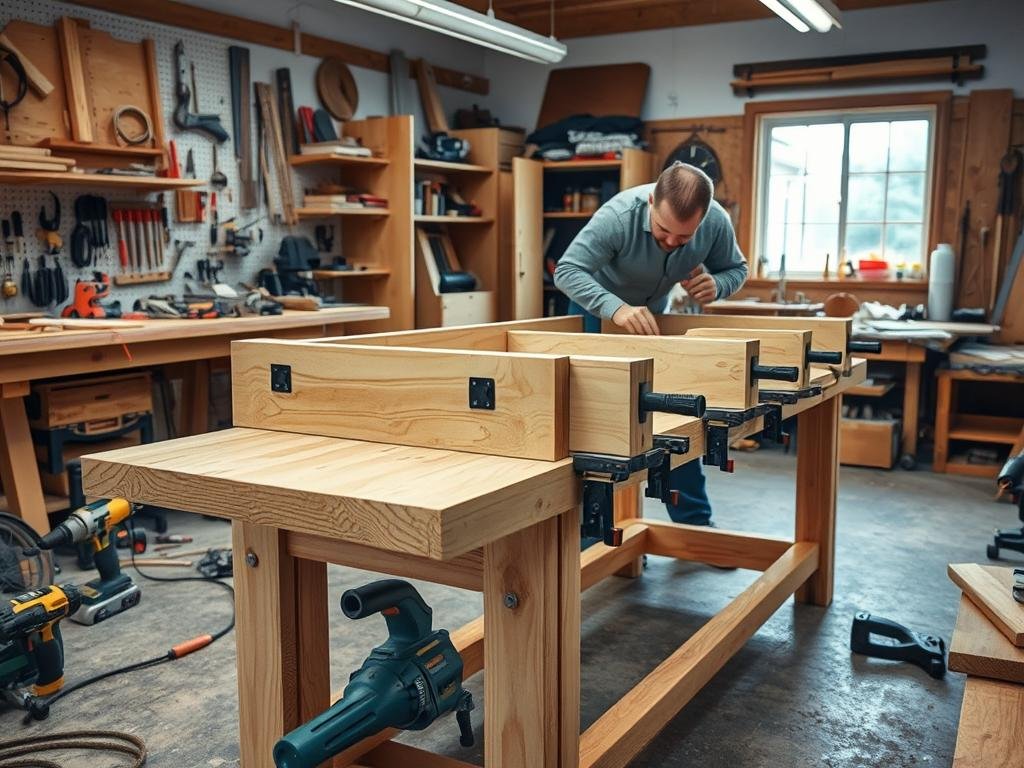
Precise Measuring and Cutting Techniques
Accuracy is crucial when working with lumber. I double-checked every measurement before making a cut. This ensured that each piece fit perfectly during assembly.
Using a circular saw, I carefully followed my measurements to avoid errors. I also marked each cut clearly to stay organized. Taking these extra steps paid off in the long run.
Here’s a quick list of tips to keep in mind:
- Measure twice, cut once to avoid mistakes.
- Use clamps to secure lumber before cutting.
- Keep your workspace clean and organized.
By following these steps, I was able to complete the build efficiently. In know you might have heard these basics hundreds of times by now, but it’s worth keeping them top-of-mind while building your workbench.
Tool | Purpose |
---|---|
Circular Saw | Cutting lumber to size |
Measuring Tape | Ensuring accurate measurements |
Clamps | Securing lumber during cutting |
You can also use these techniques with unique wood projects to begin practicing.
Building the Benchtop and Assembling Components
Creating a sturdy and functional benchtop requires precision and attention to detail. This part of the project is crucial, as it sets the foundation for the entire build. I started by milling the lumber to ensure it was perfectly flat and square. This step is essential for a stable and reliable surface.
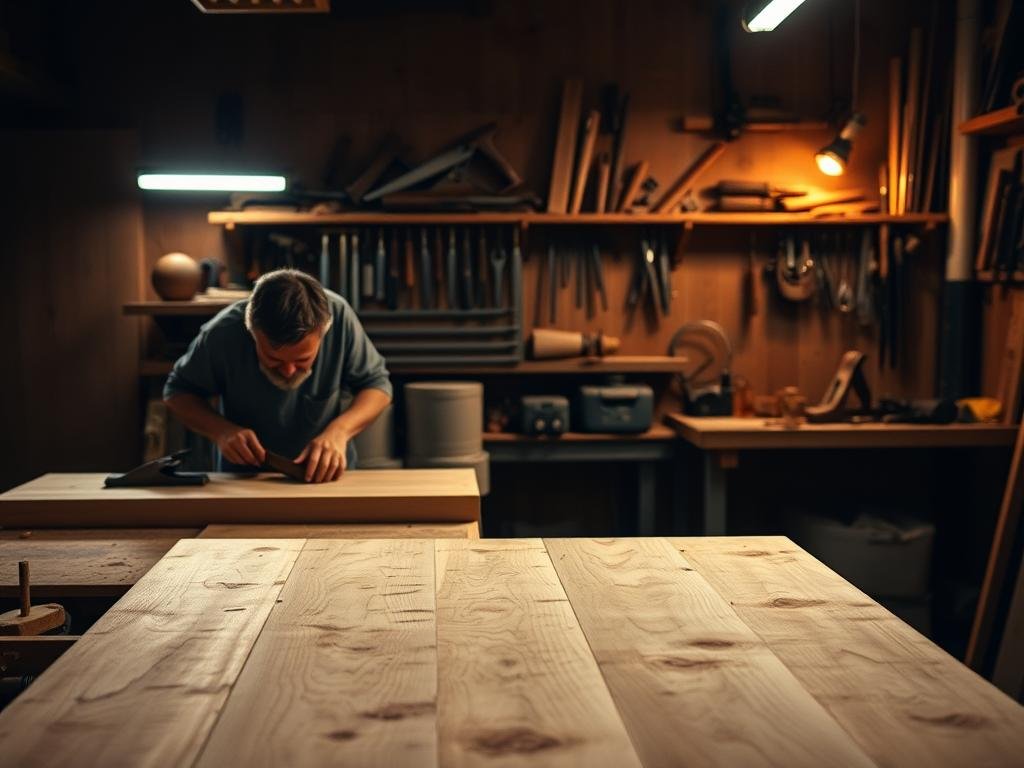
Milling, Gluing, and Dry Assembly Tactics
Milling the lumber was the first step. I used a planer to achieve a smooth and even surface. Once the pieces were ready, I moved on to gluing. Applying glue evenly and clamping the pieces tightly ensured a strong bond.
Dry assembly was next. I assembled the benchtop without glue to check for fit and alignment. This saved time and prevented mistakes during the final assembly.
Here are some tips for this process:
- Use a planer for a flat and square surface.
- Apply glue evenly and clamp tightly for a strong bond.
- Perform dry assembly to check alignment before final gluing.
Using Jigs for Accuracy
Jigs played a key role in maintaining accuracy. I created a simple jig to ensure each part was placed correctly. This helped me avoid errors and kept the assembly process smooth. Organizing my shop space was also important. Having everything in its place saved time and made the workflow more efficient.
Here’s how I used jigs:
- Built a jig to guide precise placement of components.
- Kept tools and materials organized to save time.
- Used clamps to secure pieces during assembly.
By following these steps, I was able to build a benchtop that was both sturdy and functional. Taking the time to plan and execute each step carefully made all the difference.
Installing Vises and Workholding Features
Adding vises to your workbench is a game-changer for stability and functionality. When I installed both a tail vise and a leg vise, I noticed a significant improvement in how securely my projects stayed in place. Here’s how I approached the process.
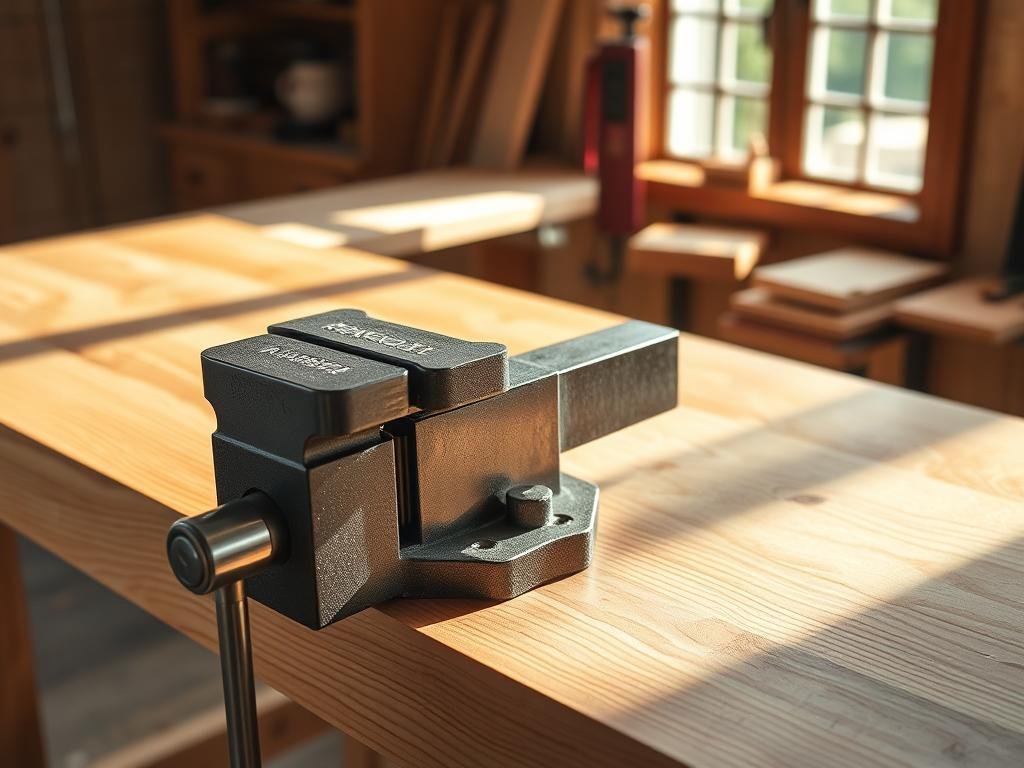
Tail and Leg Vise Installation Insights
Installing a tail vise requires precision. I started by marking the placement on the board to ensure it aligned perfectly with the workbench edge. A clear photo from the instructions helped me visualize the setup before drilling any holes.
For the leg vise, positioning was key. I used a video demonstration I found on Instagram to guide me through the steps. This was especially helpful when troubleshooting the alignment of the screw mechanism.
Here are some tips to make sure your vise assembly goes smoothly:
- Double-check measurements before drilling holes.
- Use clamps to hold the vise in place during installation.
- Test the movement of the vise before final tightening.
Choosing high-quality vise hardware can impact the overall cost, but it’s worth the investment. Sturdy boards and durable screws ensure the vises remain secure over time. Taking the time to make sure everything is aligned correctly will save you from headaches later.
By following these steps, I was able to install both vises efficiently. The result was a workbench that offered unmatched stability and versatility for my projects.
Customizing Workbench Features
Customizing your workbench can transform it from a basic tool to a personalized workspace. Adding extra features like shelves and accessories not only increases functionality but also makes the area more organized. Here’s how I tailored my workbench to fit my needs.
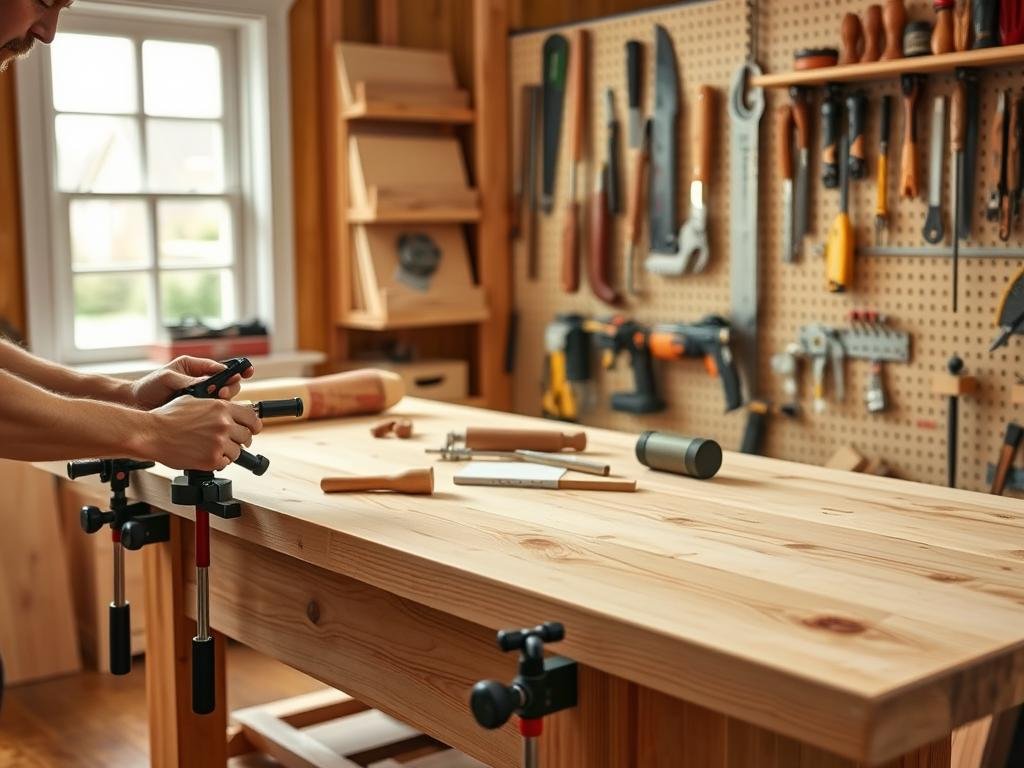
Adding Shelves and Accessories
One of the first things I did was add a bottom shelf. This provided extra storage for tools and materials, keeping my workspace clutter-free. To ensure the shelf fit perfectly, I measured the dimension of the space between the legs. Using a diagram helped me visualize the layout before cutting the wood.
For workholding devices, I drilled additional holes into the benchtop. This allowed me to attach clamps and other accessories securely. Here’s a quick guide to drilling:
- Mark the hole locations carefully to avoid mistakes.
- Use a drill press for precision and consistency.
- Test the fit of each accessory before finalizing.
Finishing Touches and Custom Finishes
Matching the finish of my workbench to the overall room was important for a cohesive look. I chose a stain that complemented the shop’s color scheme. Applying the finish evenly ensured a professional appearance.
During the assembly of customized features, I made slight adjustments to the leg configurations. This improved stability and made the workbench more user-friendly. Here’s a summary of the adjustments:
Feature | Adjustment |
---|---|
Leg Placement | Widened for better balance |
Leg Height | Leveled for even weight distribution |
By taking the time to customize my workbench, I created a tool that’s not only functional but also tailored to my specific needs. These small changes made a big difference in my workflow.
Overcoming Challenges and Budget Realities
Building a sturdy work surface on a budget taught me valuable lessons about resourcefulness and planning. One of the biggest hurdles was selecting the right tools and materials without overspending. I had to get creative to ensure quality while staying within my budget.
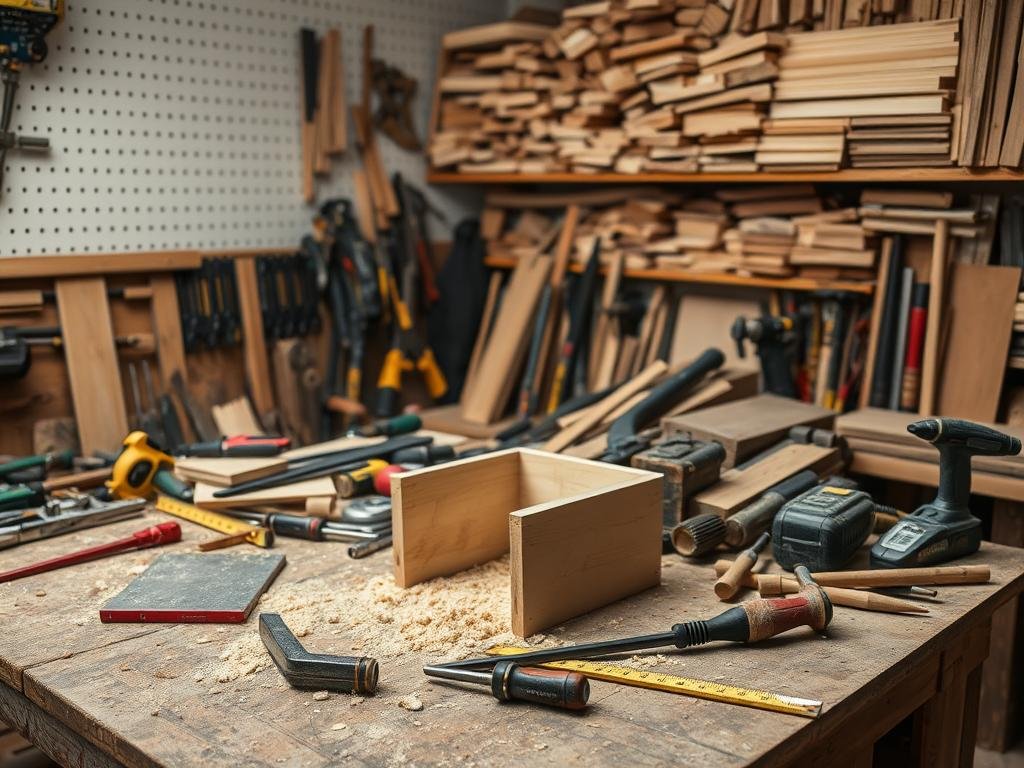
One challenge was finding the right bit for drilling precise holes. Premium options were expensive, so I opted for a mid-range bit that performed well for my needs. Another issue was assembling the stretcher and base. I used clamps and jigs to ensure everything aligned perfectly, even without professional-grade tools.
Area | Solution |
---|---|
Tools | Rent or borrow instead of buying |
Materials | Use reclaimed lumber for non-critical parts |
Hardware | Compare prices online for bulk discounts |
Proper planning also helped me avoid mistakes. I documented each part of the process with a photo to track progress and troubleshoot issues. This was especially helpful when assembling the bottom structure, where alignment was critical.
By focusing on critical areas and finding affordable alternatives, I was able to build a functional work surface without breaking the bank. These lessons taught me that careful planning and resourcefulness can overcome even the toughest budget constraints.
Tips and Lessons Learned from My Experience
Reflecting on my build, I realized how critical tool selection and maintenance were to the project’s success. Every step, from choosing the right saw to measuring cuts in inches, played a vital role. Here are some key takeaways that can help you avoid common pitfalls and achieve a sturdy, functional work surface.
Tool Selection, Jig Building, and Maintenance Tips
Choosing the right tools made a huge difference. I invested in a quality circular saw for precise cuts and a sturdy drill for creating pilot holes. A router was essential for shaping edges, and clamps ensured everything stayed in place during assembly.
Building jigs was another game-changer. A simple jig helped me align pieces accurately, saving time and reducing errors. Here’s a list of tools I found indispensable:
Tool | Purpose |
---|---|
Circular Saw | Cutting lumber to size |
Drill | Creating pilot holes |
Router | Shaping edges |
Clamps | Holding pieces together |
Maintenance is equally important. Keeping tools sharp and clean extends their lifespan. I also learned the value of using quality holdfasts for securing workpieces. Regular checks on the base and stretcher ensure long-term stability.
Lessons Learned from Each Step
Every cut, measured in inches, impacts the final product. I double-checked measurements to avoid costly mistakes. Here are some lessons I learned:
- Use a sharp chisel for clean, precise holes.
- Test-fit pieces before applying glue to ensure a perfect fit.
- Organize your workspace to keep tools and materials within reach.
By focusing on these details, I was able to create a work surface that’s both functional and durable. These tips can help you achieve similar results in your own project.
Additional DIY Workbench Ideas and Variations
Exploring creative ways to customize your workbench can elevate its functionality and fit your unique needs. Whether you’re working in a small shop or a spacious room, adapting standard designs can make a big difference. Here’s how you can modify your workbench to suit your space and workflow.
Alternative Designs and Modifications
One of the easiest ways to customize your workbench is by adjusting its dimensions. For example, reducing the depth by a few inches can make it fit better in a compact shop. Also, adding a shelf at the bottom provides extra storage without taking up valuable workspace.
Another modification is altering the height. If you’re taller or shorter than average, adjusting the legs can improve comfort and reduce strain. I found that raising my workbench by two inches made a noticeable difference in my posture during long projects.
- Adjust the width or depth to fit your shop.
- Add a bottom shelf for extra storage.
- Change the height for better ergonomics.
- Install additional holes for workholding devices.
Cost-Saving Adjustments
Customizing your workbench doesn’t have to be expensive. Using reclaimed lumber for non-critical parts can significantly reduce the cost. I saved money by repurposing old boards for the shelf and stretcher.
Another way to cut costs is by simplifying the design. This is especially handy for beginners who need to learn the basics. For example, using screws instead of mortise and tenon joints can save time and money without compromising stability. Here’s a comparison of cost-saving options:
Adjustment | Cost Savings |
---|---|
Reclaimed Lumber | Up to 30% |
Simplified Joints | Reduced labor and hardware costs |
Bulk Hardware Purchase | Discounts on screws and fasteners |
Real-Life Examples and Resources
During my build, I considered several modifications based on my shop’s layout. For instance, I added a front shelf to hold frequently used tools. This small change improved my efficiency and kept my workspace organized.
If you’re looking for more ideas, I recommend checking out detailed PDFs and video tutorials. These resources provide step-by-step instructions and inspiration for your project. By experimenting with different designs, you can create a workbench that’s both functional and tailored to your needs.
Conclusion
Building a custom work surface has been one of the most rewarding projects I’ve undertaken. From planning to assembly, every step reinforced the importance of precision and attention to detail. Following the instructions carefully, especially when placing screws and aligning legs, ensured a final result that is now the backbone of my woodworking store.
Using the right material and tools made a significant difference. Whether it was cutting lumber to size or securing pieces with clamps, each task required focus. I learned that taking the time to double-check measurements and align components properly saved me from costly mistakes.
However, I didn’t do it all on my own. I had the help of woodworking bench plans such as the ones below. It gave me the confidence to start the project, so click below to get started.
What materials do I need to build a sturdy workbench?
You’ll need lumber for the top, legs, and stretchers, along with screws, glue, and hardware like vises. Hardwood is ideal for durability, but softwood can work for a budget-friendly option.
What tools are essential for this project?
A circular saw, drill, clamps, and a measuring tape are must-haves. For precision, consider a miter saw, router, and chisels. Jigs can also help with accuracy during assembly.
How do I ensure my workbench is stable?
Focus on a solid base with sturdy legs and stretchers. Use glue and screws for strong joints, and make sure the top is securely attached. Adding weight to the base can also improve stability.
Can I customize my workbench with additional features?
Absolutely! You can add shelves, drawers, or pegboards for storage. Tail and leg vises are great for workholding, and a custom finish can protect the surface while enhancing its look.
How do I install a vise on my workbench?
Start by marking the placement on the bench’s edge. Drill holes for the vise screws and attach it securely. Use a spacer to ensure smooth operation and test it before finalizing the installation.
What’s the best way to cut lumber accurately?
Measure twice and cut once! Use a square to mark straight lines and a sharp saw for clean cuts. A miter saw or circular saw with a guide can help achieve precise dimensions.
How much space do I need in my shop for this project?
Ensure you have enough room to lay out materials and move around comfortably. A clear area of at least 8×4 feet is ideal for assembling and working on the bench.
Are there budget-friendly alternatives for materials?
Yes, you can use construction-grade lumber or repurpose old wood. Softwoods like pine are cheaper and still functional, though they may not be as durable as hardwoods.
How do I maintain my workbench over time?
Regularly clean the surface and check for loose screws or joints. Apply a fresh coat of finish as needed to protect the wood from wear and tear.
Can I modify the design to fit my specific needs?
Definitely! Adjust the dimensions, add or remove features, or use alternative materials. The design is flexible, so tailor it to your workspace and workflow.